It’s very dangerous if the operator didn’t read the manual carefully and violate the steps or regulations to operate a disc separator. Here are the requirements of how to start and stop a disc separator.
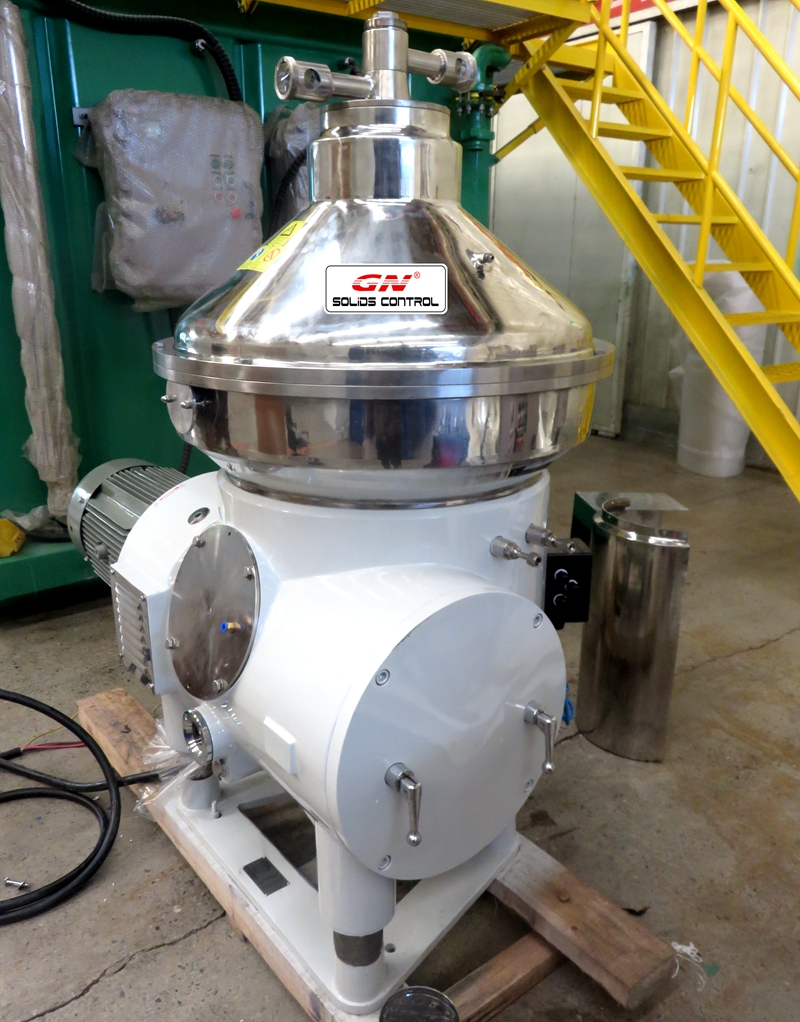
One. The material entering the disc centrifuge, which must be the lower part of the decanter centrifuge tank, should reach 65°C. It has the advantage of helping to achieve a good separation, minimizing the solid phase in the material, and slowing down the clogging inside the disc centrifuge drum. In addition, it helps to extend the disassembly and cleaning time cycle of the disc centrifuge drum.
Two. The screw pump of the disc separator should be set at a flow rate of 30 cubic meters per hour. The backflow butterfly valve on the screw pump should be open. This is because the disc centrifuge’s material supply line is fitted with a strainer. The strainer barrel will filter out the fibers and oil and mud masses but blind or block the strainer barrel. Especially when the material temperature is lower than 65℃, the oil sludge is more likely to form clumps. The blockage happens when the butterfly valve wasn’t adjusted, the flow meter shows that the flow rate soon becomes smaller; when the butterfly valve was turned a bit down, the flow meter shows that the flow rate soon becomes smaller. This shows that the filter of the strainer is blocked. At this time, the slurry supply pump should be stopped a new filter barrel should be replaced, then restart the slurry supply pump, and turn the flow rate to around 9 cubic meters per hour. The blocked strainer barrel should be cleaned up quickly and installed in time, otherwise, the material supply of the disc separator will be stopped.
Operation requirements of disc separator shutdown.
First. The decanter and the centrifuge must be cleaned inside before shutdown. The decanter needs to be stopped first, flushed, and then the centrifuge stopped and flushed. This is because, in this system, the decanter centrifuge precedes the disc centrifuge, and flushing water is relatively cleaner water than from the centrifuges.
Two. Close the ball valve of the slurry supply pipe on the inlet of the decanter centrifuge, open the valve on the flushing line of the decanter separator, turn on the flushing pump, and use flushing water for cleaning. Before flushing, lower the drum speed of the decanter to 1500 RPM and set the differential speed to 25 RPM for the best flushing effect. In addition, it is possible to flush twice with two tanks of water, due to the limitation of the water storage capacity of the disc centrifuge tank. Be sure the inside of the decanter centrifuge drum is clean. Then, turn off the pump, close the valve on the flushing pipe, and open the valve on the decanter centrifuge slurry supply pipe.
Three. The disc centrifuge continues to work until the outlet liquid position reaches 600 in the tank. Close the slurry pump, and press the partial slagging button, which will appear to make the slag current spike. You must wait for the slagging current to back down to normal; Press the partial slagging button again, and you also must wait for the slagging current to back down to normal. After that, press full slagging button once, so that the operation will empty internal material out of the disc centrifuge. The irregular operation will cause disc centrifuge motor overload and fault shutdown.
Four. Close the butterfly valve on the filter outlet pipe, open the butterfly valve on the flushing water, and switch on the flushing pump. After the flushing is completed, follow the disc centrifuge shutdown operation requirements, twice partial slagging, once full slagging, then empty the disc centrifuge rotor drum.
Five. Close the valve of the flushing pipe and open the valve on the material line so that its pipeline is in standby mode.
At last, stop the disc separator. When the drum comes to a complete off, stop the pump and turn off the power.
PS. Every day after the use of the fine shaker, use hot water to rinse, and then stop the shaker, and use tools to clean the sieve mesh surface. You must make ensure that the screen surface is clean to prevent the sediment dry on the screen surface, which could be difficult to clean, reduce the separation and spill over slurry to the outlet solid phase.
GN usually provides disk separators with centrifuges together with pumps. Besides, pumps and mud tanks are sometimes necessary. If you want more information, please visit: gnsolidscontrol.com